Early (2011-2013) United States Nissan Leaf’s had a “limit charging to 80%” feature in the dash. Nissan removed this feature from US cars after the EPA ruled that if the feature remained, they had to report a lower battery range because on average the car would not be fully charged when it left. [This ruling was incorrect in my opinion…but Nissan removed the feature so that they could advertise the EPA range based upon a 100% charge of the battery.]
I, and many other people, still like to limit charging to only 80% of the battery total capacity in an effort to extend the life of our EV batteries. [This extra effort may or may not be worth the trouble, and many people advise to just charge to 100% and not worry about your battery health, especially for 2016+ vehicles which have a longer battery warranty. But I like to limit charging of Lithium Ion batteries to 80% if I don’t need the extra range.]
If you wanted to only charge your Nissan Leaf to 80% (unless you need extra range for longer trips) on a regular basis, how can you do it on later model year vehicles?
There are three options that I know of:
1. The only way to get a similar effect (keeping the car below 80% SOC most of the time) using only inbuilt features (i.e. without spending extra money) is to set up the charging timer to charge your vehicle right before you leave. This only works well if you have a regular departure time each day (e.g. for a static work schedule). Then, when you plug in the car, it will not charge until a few hours before your scheduled departure time, aiming to reach 100% about 30 minutes before you depart. This means that the time the battery sits at 100% is minimized. [If you are clever, you can lie about your departure time so that it is reaching 80% about the time you actually leave…]
The downside is that your vehicle is not “ready to go” if you need to leave for an unplanned trip before your regularly schedule departure time, and if you want to charge any other time you have to remember to disable the charging timer so that it will actually charge when you plug in. [My 2015 leaf has an easy to use button for disabling the charge timer…]

So this can be made to work if you have a regular schedule, but it can also be annoying.
2. You can “mimic” the “charge only to 80%” feature by using a Smart / connected EVSE that has a charge limiter built in. For example, I have a JuiceBox, and when I plug in my 2015 leaf, I use the phone app to set the “plugged in percentage” and “stop percentage” (which I just leave at 80%) and it estimates the amount of power needed and will shut off charging after that amount is used. This requires that you pay money for a smart EVSE…but if you haven’t already purchased an EVSE, getting a “smart” or “connected” one with a similar feature will probably only add 1-2 hundred dollars to the purchase price.
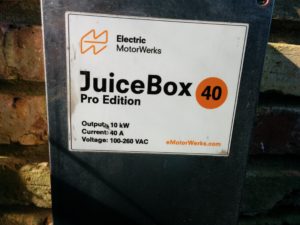
3. There is also a 3rd party add-on box you can install in your vehicle called Open Vehicle Monitoring System (hardware device) that would allow you to set a charge % limit and also do things like pre-heat in the winter remotely, and has a lot of other logging features…. but it costs $260 (and if you want to be able to use it on a cellular network away from your home/work WiFi networks or the bluetooth range of your phone, you need to include a SIM card with data capabilities which will also probably have a monthly fee)
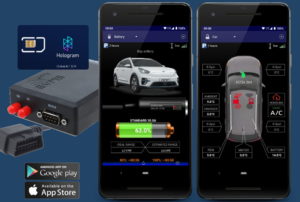
Because I already had a JuiceBox, I use method 2…but if I already had a non-smart EVSE, I would probably go with the OVMS route, as it adds other features to the car.
[Especially since the Nissan Connect system in my 2015 leaf no longer works as it used an older 2G cellular service that has since been retired.] If you have a brand new Nissan Leaf, it probably includes the Nissan Connect service, at least for the first three year of car ownership.