When hurricane Irma threatened Florida, I was not worried about the food in my fridge going bad or scrambling to buy ice, because I had an inverter in my garage hooked up to a 12 volt battery made up of two golf cart batteries. With new batteries, this setup would provide around 2 kWh of backup power, although I’m currently using 4 year old batteries that had previously seen 400 cycles of use in an electric vehicle, so the actual performance is closer to 0.6 kWh (600 Watt/Hours).
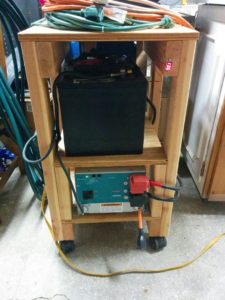
Our energy star fridge/freezer draws around 240 watts of power when running the compressor, although the average energy draw is lower as the compressor shuts off once it reaches temperature. So the golf cart batteries alone would be enough to power my fridge for 2.5 hours of continuous cooling, or 5-8 hours of typical usage assuming the fridge wasn’t having to work super hard to cool things off.
When Irma hit, we lost power at 1am on Monday were without power until 5pm on Wednesday, or around 64 hours. However, I only ran my backup system for 31 of those 64 hours. I first hooked the system up around 1pm on Monday, and ran it until 10pm. I shut it down overnight when I was sleeping and ran it around 11 hours each on Tuesday and Wednesday during the day. My fridge was easily able to keep things frozen/cold overnight and “catch up” during the days (I had loaded the freezer up with a lot of frozen water, and the fridge with a lot of chilled water well before our outage occurred).
Over the 31 hours I ran the system, we averaged 190 watts of draw per hour (or 5890 watt / hours or 5.89 kWh total), which is significantly larger than the 0.6 kWh the golf cart batteries could provide alone. This draw was primarily from our fridge, although we also used 20-50 watts of power to keep our DSL wifi-router running and charge personal electronics, as well as running the power hungry microwave for a few minutes at a time.
To augment the stored power in the golf cart batteries, I wired them in parallel with the 12 volt accessory battery on my electric truck (which has a 20-22 kWh battery pack). By leaving the ignition of my truck turned on, I enabled my 500 watt DC2DC converter which continuously charges the 12v accessory pack from the main (LiIon) battery pack. Because the 500 watt DC2DC converter was providing well more than the 190 watt average draw, the system worked well.
The golf cart batteries acted as a “buffer”, providing extra power to the (2000 watt) inverter if needed. [For example, when I used our 1300 watt microwave to heat up food for 5 minutes here and there.] And the golf cart batteries were topped up by the 12 volt system on the truck, ultimately powered by the main traction pack.
One big advantage is that the system is nearly silent, generating only a slight hum from a fan in the inverter that becomes inaudible as you walk away from it. It also has no danger of producing deadly carbon monoxide, which has already killed several people in Orlando due to mis-using gas burning generators.
It took 8.34 kWh to recharge my truck after the outage was over, so my overall system efficiency (power provided / power required to re-charge) is 70%, which isn’t bad considering the parasitic losses from keeping all of the truck’s systems active, the losses from the DC2DC converter going from 120v DC to 12 vDC, and the inverter going from 12v DC to 120 v AC, heat losses, etc.
So it looks like I could easily ride out a 5-6 day power outage before needing to find a generator or EVSE to re-charge the truck (And we haven’t even tapped the Leaf’s battery pack yet….there are commercial offerings for that.). One advantage of having your battery pack inside a vehicle is that you can drive it elsewhere to recharge. An EVSE located two miles away from me had power starting on Tuesday, so I wasn’t worried about being able to recharge my truck…